Dry Gas Seals
Reducing gas leakage
Depending on the diameter of the rotor, work pressure, temperature of the packed gas and the frequency of the rotor speed, the leakage through every DGS can be from 0,01 to 0, 15 m3/min.
Although the value is equivalent to the intensity of the leakage through the oil seals, need to consider that at installed oil seals an additional gas leakage occurs from degassing of circulating oil. Usually gas from oil is released into the atmosphere, doubling the total volume of leakage through the seal up to 6 m3/min.
Reduction of the energy consumption
At dry gas seals installation the pumping systems for oil circulating are excluded, consuming the electricity, and hence the energy is saved. The power consumption of the oil seals is from 50 to 100 kW, while the losses do not exceed 5 kW in DGS.
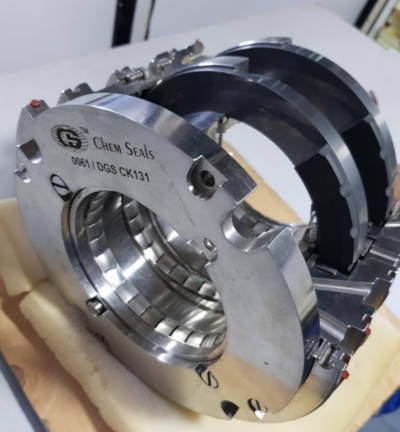
Exclusion of oil leakages
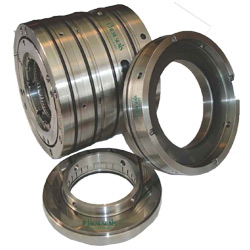
Replacement of oil seals into dry eliminates seal oil leakage in the flow part of the compressor and that is why there is no gas pollution and the pipeline's technical characteristics deterioration.
Less volume of maintenance
Dry gas seal systems have low time spending on maintenance, because they do not have assemblies, which are necessary at the oil circulation (pumps, control valves, relief valves) in comparison to oil seal systems.
Simplification of the software system
DGS systems do not require the installation of sophisticated components, which provide oil circulation, and devices for its processing and cleaning.
Higher reliability
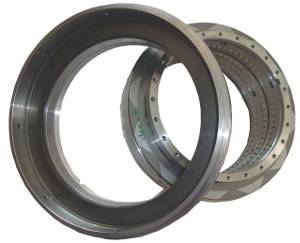
Most of idles of compressor with oil seals caused by problems in the sealing system.
Short term of payback
The term of payback of DGS systems in average is from 12 to 16 months. If there is a trend of the prices increase on energy sources the term of payback will reduce.